PRODUCTS
Ultrasound Measurement Instrumentation and Services
MCT CAVITATION METER
Measure the Cavitation Performance
The MCT-2000 combines the power of a high speed digitizer, spectrum analyzer, and advanced microprocessor to produce an acoustic pressure spectrum. Different components in the spectrum are analyzed to quantify the fundamental frequency and pressure from the direct field, stable cavitation, and transient cavitation. Specifically, the pressure within the fundamental frequency peak represent the direct field pressure from the sound wave. The harmonics, sub-harmonics, and ultra-harmonics represent the stable cavitation, or the cavities that oscillate in size and dimension. Finally, the broadband white noise in the spectrum represent the transient cavitation, or the cavities that implode and collapse.
MCT PRESSURE METER
Acoustically Test Ultrasonic Cleaning Tanks
The HCT hydrophone with MCT-1200 Digital Pressure Meter is a trustworthy instrument to characterize and monitor the relative acoustic properties of ultrasonic cleaning systems. Its unique single point sensing design allows localized measurements to generate true 3-dimensional acoustic maps of the cleaning tank.
Some other key features include:
- Parameters: F0 and PTOT
- Data logging
- Self-Calibration to MCT-2000
- Touchscreen
- Real-time data transfer for continuous monitoring
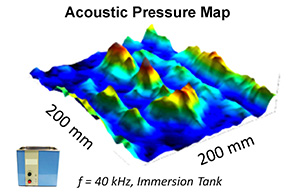
For many ultrasonic cleaning processes, achieving a uniform acoustic field is challenging. This is because there is a broad range of process variables that affect the acoustic field distribution including transducer-to-transducer variation, gas concentration, temperature gradients, flow rate, among others. Ultimately, this contributes to how well particles are removed directly affecting process yield.
NPL CAVIMETER
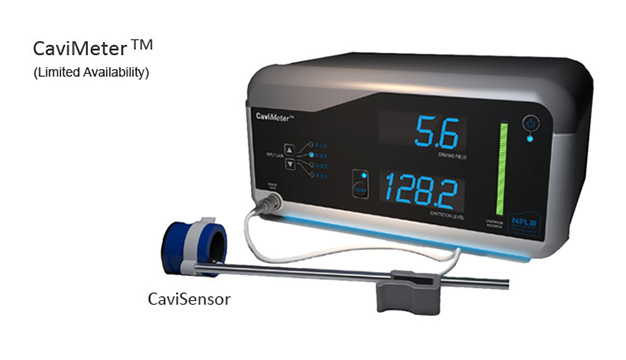
Measuring Acoustic Cavitation
Ideal for measuring acoustic cavitation in ultrasonic wafer cleaning tanks, the CaviMeterTM was developed by the National Physical Laboratory (NPL) to measure the acoustic emissions generated by cavitation. Cavitation is the growth, contraction, and collapse of micro-bubbles (or cavities) within a liquid media in response to a driving ultrasonic field. The amount of energy from the implosion of a cavity is sufficient to overcome particle adhesion forces and hence is used for ultrasonic cleaning and other sonoprocessing applications such as semiconductor wafer processing. Excessive cavitation energy can also damage the silicon surface and films of a wafer substrate, which makes it essential to develop and control a process window through careful measurement.
How Cavitation Measurements Work
The unique CaviSensor cavitation detector is designed to measure both the broadband acoustic signal generated from cavitation and the direct field at the drive frequency in the ultrasonic cleaning tank. The hollow cylindrical shaped sensor is constructed with a polyurethane shell lined with a piezoelectric polymer film. While the polyurethane “shields” the high frequency broadband signals (High Frequency, or HF) generated by cavitation outside the cylinder, the piezoelectric film detects the localized cavitation along the inner central line of focus. The piezoelectric film also measures the direct field signal at the fundamental frequency (Low Frequency, LF), which is transmitted through the polyurethane. Both the HF and LF signals are then processed by the CaviMeterTM cavitation measuring system to quantify the level of cavitation and direct field pressure.
CTS SCANNER
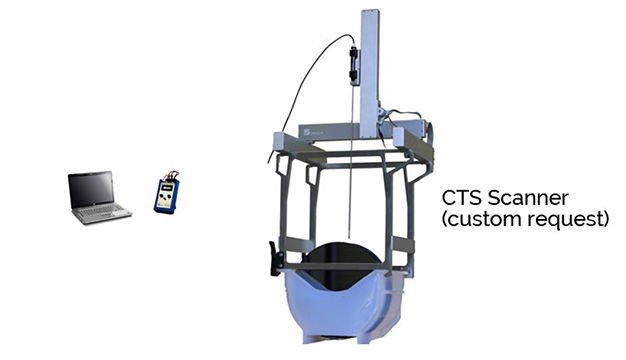
Automate Hydrophone Scanning
The CTS Scanner enables hydrophone mapping to be done automatically, using the HCT hydrophone. The scanner is customized to mount to substrate carriers, eliminating the need for positioning alignment. Because the shaft diameter of the HCT hydrophone is only ~3 mm, 2D acoustic plots can be acquired in loaded configurations to simulate actual conditions in the cleaning process (e.g., between substrates for semiconductors, data storage, and related applications).
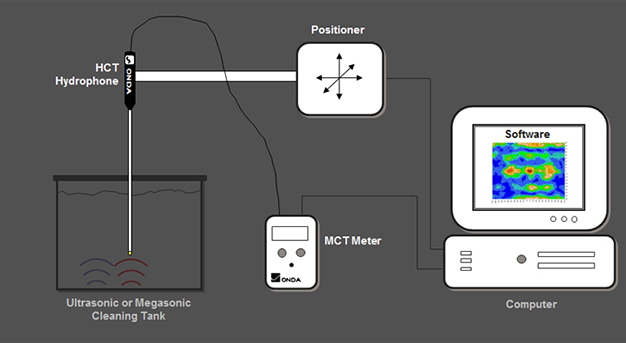
Applications
- Acquire acoustic maps to optimize cleaning efficiency of ultrasonic and megasonic baths
- Routinely spot check acoustic field of cleaning tank for process control monitoring
- Compare tank-to-tank performance to maintain matching in production environments
- Develop and tune process recipes by determining the acoustic effects of varying chemistries, loading conditions, and power settings.
- Identify cleaning tank issues such as debonded or malfunctioning transducers
- Collect lower level acoustic information by connecting probe directly to an oscilloscope
Acoustic Pressure Plot of a 970kHz Semiconductor 200mm Single Wafer Cleaner indicating near field and standing wave effects